Essential Free Tips for Resolving ISO 9001 Certification Non-Conformities
In the process of ISO 9001 Certification non-conformities are defined as deviations from the specified requirements that could result from many sources like customer feedback, audits or internal audits. Successfully addressing these issues is not just about ensuring compliance with ISO 9001 standards but also helps to ensure constant improvement within the company. Resolving issues quickly and efficiently can prevent repeat occurrences, improve efficiency in operations, and ultimately result in better customer satisfaction.
Get Business Development Kit
Understanding Major Non-Conformities
Non-conformities are typically classified into two categories: minor and major. Major non-conformities could severely affect the company’s ability to satisfy customer demands and maintain customer compliance. Minor infractions, on the other hand, are not as severe and may result in a change that does not immediately impact the quality of service or product; however, they still require actions to avoid escalating.
Some Major Non-Conformities
– Absence of a documented procedure as required for ISO 9001 Certification
-Failure to implement a crucial QMS process
-Significant breaches in adherence to the requirements of regulatory agencies
-Customer’s repeated complained about the same problem
– Lack of evidence for MRM
– Issues related to the delivery of services or products
– Absence of corrective actions to address Non-Conformities
– Documentation and records-keeping related issues
– Significant deviations from quality targets
– Poor risk management practices
– Inability to meet expectations of the customer
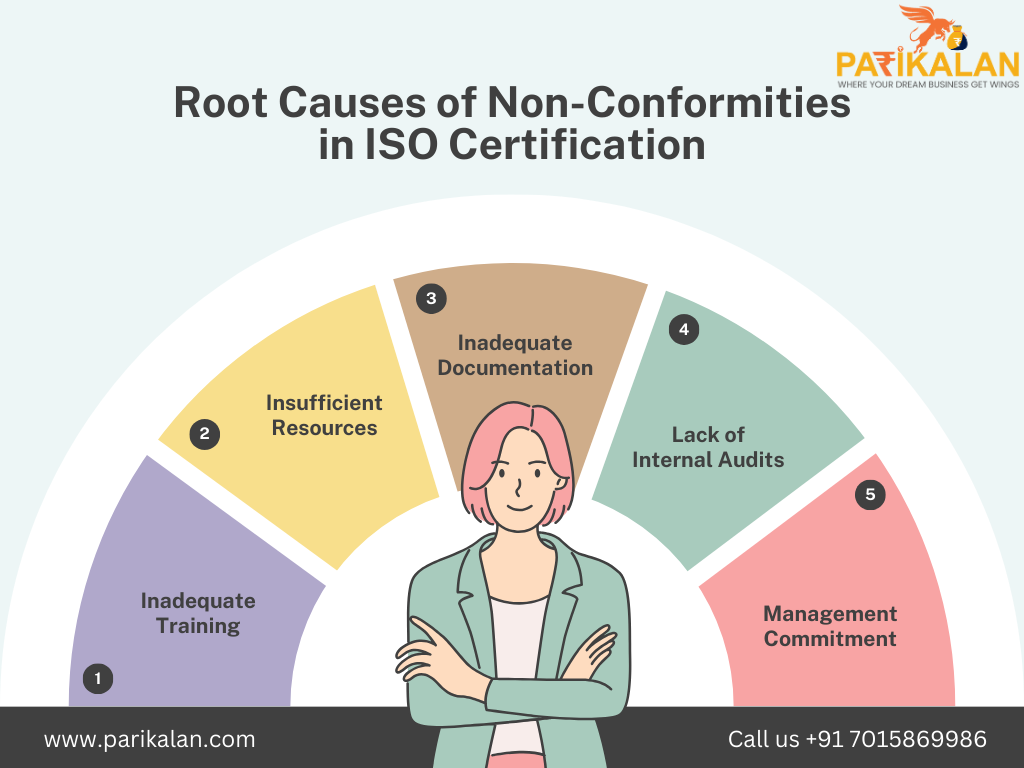
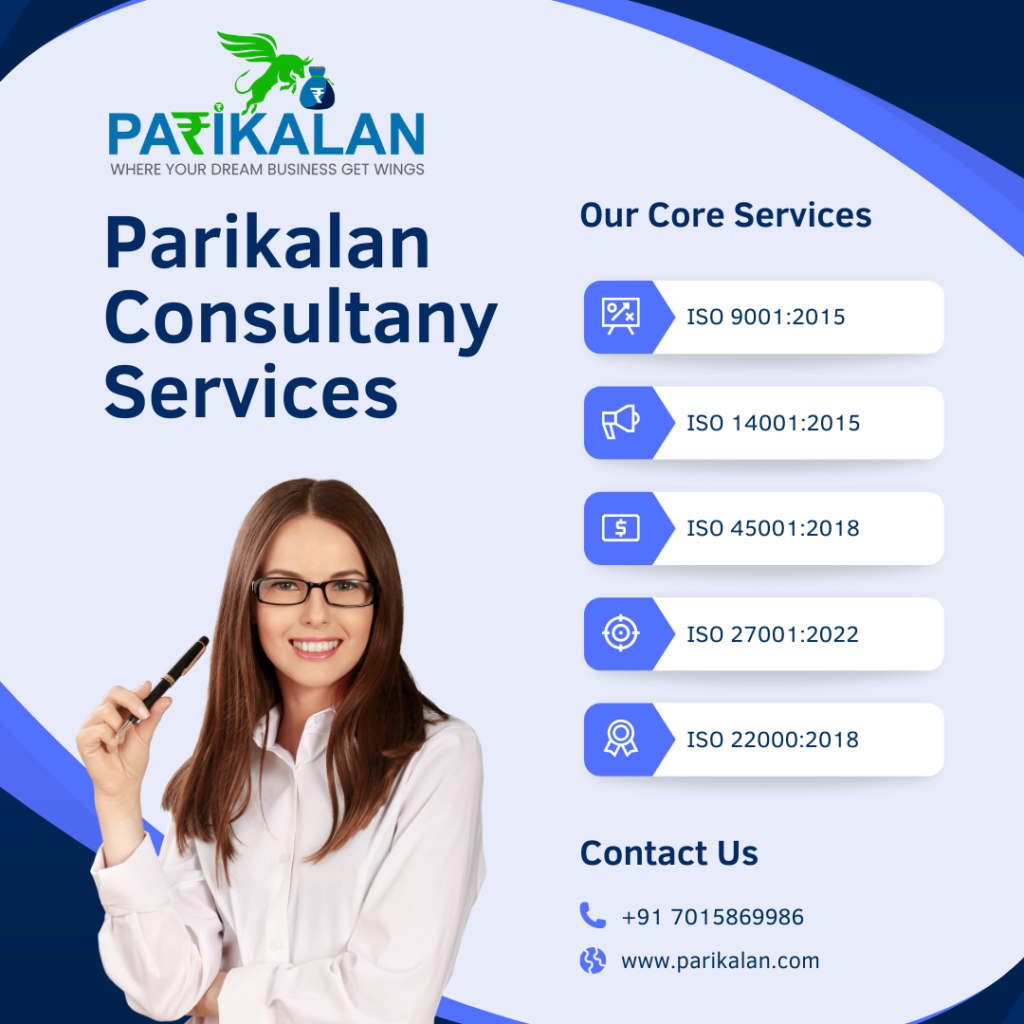
Understanding Minor Non-Conformities
Some Minor Non-Conformities
– incorrect documentation
– Minor mistakes in the training record
– Sometimes, delays are encountered in the conduct of internal audits
– Examples of storage or handling that is not properly handled of items
– A few small mistakes in labeling or packaging
-Issues with communication or information
– Minor delays in the implementation of corrective actions
– Customer feedback not being recorded properly, etc.
Are You Looking To Enhance Your Business Credibility And Quality Standards ?
Documenting Non-Conformities and Implementing Corrective Actions
Documentation should be thorough and contained. Documentation ensures transparency, allows for extensive analysis, and assists in formulating corrective measures. Tools like non-conformity reports, logs, and tracking systems can standardize documentation. Records’ accuracy will enable companies to monitor trends, evaluate the efficacy of corrective actions and help with ongoing improvement efforts.
Start by creating a thorough action plan that outlines the required steps, accountable parties, and deadlines. Make sure that all the stakeholders involved are aware and educated when necessary. The availability of funding and resources is essential to ensure you have enough time, budget, personnel, and funds to deal with the problem in depth. After implementation, keep track of the progress regularly through follow-up audits, performance reviews or status conferences. Track progress using the tracking system to monitor progress.
Tools to track progress and pinpoint any issues early. Modify the action plan in case of unexpected problems. Continuous monitoring and communication assure you that the actions taken to correct them are efficient and lasting, preventing repeating the same issue and ensuring continual improvement within the Quality Management System (QMS)/ ISO 9001 Certification process.
Documents Required for Applying ISO 9001 Certification
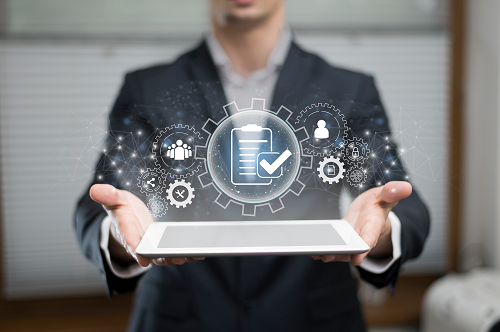
Company / Service Govt. Registration Proof

Valid Letter Head including Address
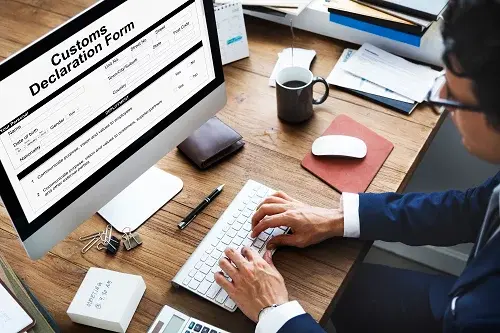
Quality Manual
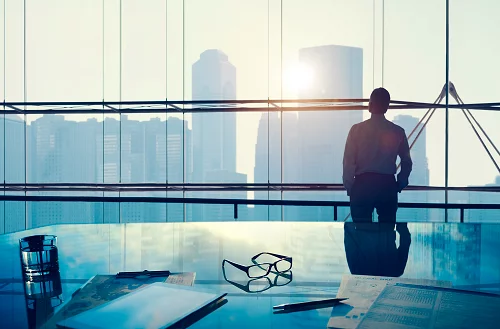
Internal Audit/MRM
Verifying Effectiveness
Examining the effectiveness of corrective measures is crucial to ensure that the non-conformities have been removed and don’t recur. This is a way to confirm that the corrective actions have addressed the root of the issue and streamlined the procedure. Methods to verify this include follow-up audits to determine if the corrective measures are correctly implemented and functioning as intended, as well as a review of performance that evaluates important metrics and results.
If the verification results show that the corrective actions are not working, changes must be made. This may mean reviewing the root cause analysis, altering the action plan or allocating more resources. Continuously adjusting and checking is crucial to sustain improvement and to ensure long-term conformance to ISO 9001 standards.
Conclusion :
Effectively handling non-conformities is the foundation of a solid ISO 9001 Quality Management System. Implementing corrective measures with sufficient resources and evaluating their effectiveness is crucial to avoid recurrence and to drive the pursuit of operational excellence. Furthermore, using non-conformity data to spot patterns and then incorporating the lessons learned into the processes improves overall customer satisfaction and quality.
If you are a business looking for expert advice to achieve and maintain ISO 9001 certification, Parikalan Consultancy OPC. Ltd., situated within Bahadurgarh, Haryana, offers extensive consultation services. Their team of experts provides
- customized assistance in the implementation of ISO standards,
- performing internal audits and
- making sure that the corrective action procedures are effective.
Working with Parikalan Consultancy can help streamline your path to ISO 9001 certification and ensure constant quality improvement.